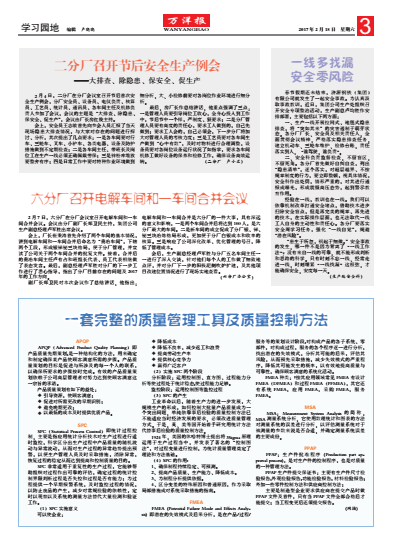
一套完整的質量管理工具及質量控制方法
APQP
APQP(Advanced Product Quality Planning)即(ji)產品質(zhi)量(liang)先(xian)期策(ce)劃(hua),是一種結(jie)構化的(de)方法,用來確(que)定和制(zhi)定確(que)保某(mou)產品使顧(gu)(gu)客(ke)滿意(yi)所需的(de)步(bu)驟。產品質(zhi)量(liang)策(ce)劃(hua)的(de)目標(biao)是促進與所涉及的(de)每(mei)一個(ge)人的(de)聯系,以(yi)確(que)保所要求的(de)步(bu)驟按時完成。有效的(de)產品質(zhi)量(liang)策(ce)劃(hua)依(yi)賴(lai)于(yu)公司高層管(guan)理者對(dui)努力(li)達到使顧(gu)(gu)客(ke)滿意(yi)這一宗旨的(de)承諾。
產品質量策(ce)劃有如下的益處:
◆ 引導(dao)資源(yuan),使顧客滿意;
◆ 促進對所需更改的早期識別(bie);
◆ 避免晚(wan)期更改;
◆ 以最低的(de)成(cheng)本及時提供優質產品。
SPC
SPC(Statistical Process Control)即統計過(guo)程(cheng)控制,主要是指應用統計分析技(ji)術對生(sheng)產過(guo)程(cheng)進行適時監控,科學區分出生(sheng)產過(guo)程(cheng)中產品質(zhi)量的隨機波(bo)動與(yu)異常波(bo)動,從(cong)而對生(sheng)產過(guo)程(cheng)的異常趨勢(shi)提(ti)出預警(jing),以便生(sheng)產管理人(ren)員及時采取措施,消除異常,恢復(fu)過(guo)程(cheng)的穩定(ding)從(cong)而達到提(ti)高和(he)控制質(zhi)量的目的。
SPC非常適用(yong)于(yu)重復(fu)性的(de)生產(chan)過(guo)程,它能夠幫(bang)助組織對過(guo)程作出可靠的(de)評估,確定(ding)(ding)過(guo)程的(de)統計控(kong)制界限判斷過(guo)程是(shi)否(fou)失控(kong)和(he)過(guo)程是(shi)否(fou)有能力;為過(guo)程提供一(yi)個早期報警系(xi)(xi)統,及時(shi)監控(kong)過(guo)程的(de)情(qing)況,以防止廢品的(de)產(chan)生,減少(shao)對常規(gui)檢驗的(de)依(yi)賴性,定(ding)(ding)時(shi)以觀察(cha)以及系(xi)(xi)統的(de)測(ce)量(liang)方法(fa)替代大量(liang)檢測(ce)和(he)驗證工作。
(1)SPC實施意義
可以使企業:
◆ 降低成本
◆ 降低不良率,減少返工和浪費
◆ 提高勞動(dong)生產(chan)率
◆ 提供核心競爭力
◆ 贏得廣泛客(ke)戶
(2)實施SPC兩個階段
分析階段:運用控制圖(tu)、直(zhi)方(fang)圖(tu)、過程(cheng)(cheng)能力(li)(li)分析等使過程(cheng)(cheng)處于統計(ji)穩(wen)態,使過程(cheng)(cheng)能力(li)(li)足夠(gou)。
監(jian)控階段:運(yun)用(yong)控制圖等監(jian)控過(guo)程
(3)SPC的產生
工(gong)業(ye)革命以后(hou),隨著生(sheng)產力(li)的(de)進一步發展,大規模(mo)生(sheng)產的(de)形成,如何控制大批量產品質(zhi)(zhi)量成為(wei)一個突出問題,單純依靠(kao)事后(hou)檢驗的(de)質(zhi)(zhi)量控制方法已不能適應當時經濟發展的(de)要求,必須改進質(zhi)(zhi)量管理(li)方式(shi)。于是,英、美等國開始著手研究用統(tong)計方法代(dai)替事后(hou)檢驗的(de)質(zhi)(zhi)量控制方法。
1924年,美國的休哈特博士(shi)提出將3Sigma原(yuan)理(li)(li)運(yun)用于(yu)生產(chan)過程當(dang)中(zhong),并(bing)發(fa)表了著名的“控(kong)制圖(tu)法(fa)”,對過程變量(liang)進行控(kong)制,為統計質(zhi)量(liang)管理(li)(li)奠定了理(li)(li)論和方法(fa)基礎。
(4)SPC的作(zuo)用:
1、確(que)保制(zhi)程持續穩(wen)定、可(ke)預測。
2、提高產品(pin)質量、生(sheng)產能力、降低成本。
3、為制程分析提(ti)供依(yi)據。
4、區分變差的特殊原(yuan)因(yin)和普通(tong)原(yuan)因(yin),作為采取(qu)局部措施或對系統采取(qu)措施的指南。
FMEA
FMEA(Potential Failure Mode and Effects Analysis)即潛在的(de)(de)失(shi)效(xiao)(xiao)模式(shi)(shi)及后果分(fen)析(xi),是在產(chan)(chan)品/過(guo)程(cheng)/服務等(deng)的(de)(de)策劃設計(ji)階段,對構成產(chan)(chan)品的(de)(de)各子系統、零部件,對構成過(guo)程(cheng),服務的(de)(de)各個程(cheng)序逐一進行分(fen)析(xi),找出(chu)潛在的(de)(de)失(shi)效(xiao)(xiao)模式(shi)(shi),分(fen)析(xi)其(qi)可(ke)能的(de)(de)后果,評估其(qi)風險,從(cong)而預先(xian)采取措施(shi),減少失(shi)效(xiao)(xiao)模式(shi)(shi)的(de)(de)嚴重程(cheng)序,降低其(qi)可(ke)能發生的(de)(de)概率,以有(you)效(xiao)(xiao)地提(ti)高(gao)質量與可(ke)靠性(xing),確保顧客滿意的(de)(de)系統化活動(dong)。
FMEA種(zhong)類:?按其(qi)應用領域常見(jian)FMEA有設(she)計FMEA(DFMEA)和(he)過程FMEA(PFMEA),其(qi)它還有系統FMEA,應用FMEA,采(cai)購(gou)FMEA,服務(wu)FMEA。
MSA
MSA:Measurement System Analysis的簡稱,MSA測(ce)(ce)量(liang)系(xi)統(tong)(tong)分(fen)析(xi),它(ta)使用數理統(tong)(tong)計和圖表的方法對(dui)測(ce)(ce)量(liang)系(xi)統(tong)(tong)的誤差進(jin)行分(fen)析(xi),以評(ping)估測(ce)(ce)量(liang)系(xi)統(tong)(tong)對(dui)于被測(ce)(ce)量(liang)的參數來說(shuo)是(shi)否合適,并確定測(ce)(ce)量(liang)系(xi)統(tong)(tong)誤差的主要成(cheng)份。
PPAP
PPAP:生(sheng)產件批準程序(xu)(xu)(Production part approval process),是(shi)對生(sheng)產件的控制程序(xu)(xu),也是(shi)對質量(liang)的一種管理方法。
PPAP生產(chan)件(jian)提交保證書:主要有生產(chan)件(jian)尺寸檢驗報(bao)告(gao)(gao),外(wai)觀檢驗報(bao)告(gao)(gao),功能檢驗報(bao)告(gao)(gao),材料檢驗報(bao)告(gao)(gao);外(wai)加一些零件(jian)控制(zhi)(zhi)方(fang)法(fa)和供(gong)應商控制(zhi)(zhi)方(fang)法(fa);
主要是制造型企業要求(qiu)供應商在(zai)提交產品時(shi)做PPAP文(wen)件(jian)及首件(jian),只有當(dang)PPAP文(wen)件(jian)全部合(he)格(ge)后才能提交;當(dang)工程變(bian)更后還(huan)須提交報告(gao)。